This project was a new build waterproof concrete basement with aesthetic facing concrete throughout several courtyards. Beautiful Basements was asked to provide 3D & waterproofing design, complete build, and waterproofing installation. The basement contains master bedroom and a sunken courtyard.
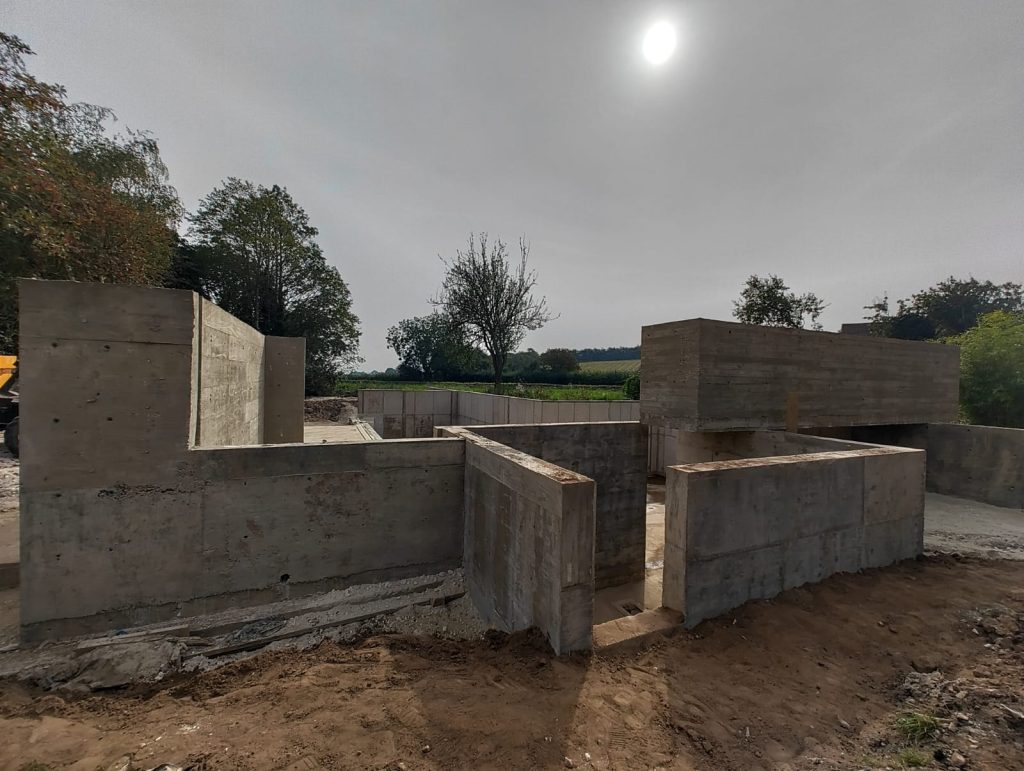
Project with facing concrete overview
Project Details
Categories: | |
Client: | Viridis Building Services |
Location: | Maplebeck, Nottinghamshire |
Surface Area: | 100 Square metres |
Completed: | 2023 |
Architect: | EngineersHRW |
Stage 1 – Project preparation - 3D design, sample walls & excavation
Design preparation
Planning conditions stated that before any work could begin the contemporary facing concrete design must be demonstrated and agreed upon. Beautiful Basements was commissioned to create a 3D design mock-up of the project and cast test panels in place to demonstrate how the facing concrete would look. Watch the video of the 3D design here.
Excavation
With the design complete and planning permission granted the build program could begin. The basement was excavated, banks made safe and base blinded with concrete to create a clean and safe place to work.
Stage 2 – Constructing the basement
When the excavation had been completed and made safe, the construction of the waterproof concrete basement with aesthetic facing concrete began.
Main slab & insulation
Prior to pouring the concrete, a layer of insulation was placed on the ground to prevent heat loss and moisture infiltration. This insulation not only enhances energy efficiency but also provides a barrier against cold temperatures, crucial for maintaining a comfortable and dry basement environment. Once the insulation is laid, the two sumps (foul and ground water) are installed and steel reinforcement bars were positioned to reinforce the concrete slab, ensuring structural integrity, and preventing cracking. Finally, the waterproof concrete was cast and levelled. As the concrete cures, it forms a solid and durable foundation for the basement space, offering stability and insulation against external elements as well as the primary defence from water ingress.
Basement walls
Casting waterproof concrete basement walls with expanding waterbar involves meticulous attention to detail to create a resilient barrier against water intrusion. Before pouring the waterproof concrete, the slab kicker is treated with a cementitious waterproofing slurry and an expanding waterbar was placed within the forms to provide additional waterproofing protection. These waterbars are designed to expand when exposed to moisture, effectively sealing any potential gaps or cracks that may develop over time. Steel reinforcement is carefully integrated into the waterproof concrete structure to provide strength and durability and reduce cracking. Throughout the casting process, measures are taken to ensure proper compaction and curing, minimising the risk of cracks, and improving the overall integrity of the walls.
Stage 3 – Facing concrete & waterproofing
Facing concrete
One of the design features of the basement was to have several areas of exposed facing concrete. With the structure of the basement complete, the areas designed to be exposed were created.
Insulation was placed behind the internal walls to increase the efficiency of the space. Shuttering had to be adjusted to include facing timber panels that would leave a print on the facing concrete.
All shuttering was propped and finally the walls cast with even more attention paid to the vibration, placement and compaction to ensure the facing concrete finish was even and consistent.
Waterproofing
The waterproofing regime on this project had to include a dual-protection system to satisfy the requirements of the warranty provider. Beautiful Basements was the designer and installer for both systems.
Primary System
Type B – Integral protection
All external walls, all concrete slabs (lower and upper ground floors) are cast with concrete including a waterproof additive. The steel reinforcing within this structure was designed to reduce the cracking to less than 0.3mm, also providing integral protection. Construction and day joints have a crystalising waterproofing slurry and an expanding waterbar applied to them to waterproof natural weak points.
Secondary System
Type C – Drained cavity protection
At the base of all external walls a recessed concrete channel was created within the slab. External walls and the floor are lined with a cavity drainage membrane (CDM). Those membranes were linked to a sump chamber via the recessed perimeter channels. Within the sump are two pumps and a high-level alarm. The whole system is designed to catch any water that is not stopped by the primary system and discharge it automatically. Flushing and maintenance points were installed to allow future servicing of the system.
Both waterproofing systems were designed by Structural Surveyors in Structural Waterproofing (CSSW) in accordance with BS8102:2009
All waterproofing materials were supplied by Triton Systems Ltd